Golfing News & Blog Articles
COBRA Releases Fully 3D Printed LIMIT3D Irons
Let’s start with the headline.
The COBRA LIMIT3D irons are the first commercially available 3D printed irons.
Because this isn’t my first day on the internet, I know some of you will read this and think (or scream in my comment section), COBRA is ripping-off Avoda, the small brand that recently received some attention for 3D printing irons for Bryson DeChambeau.
C’mon, guys. It’s not like 3D printing a golf club is as simple as hitting the print button. Well, I suppose the act itself is exactly that easy but the button doesn’t work without years of development.
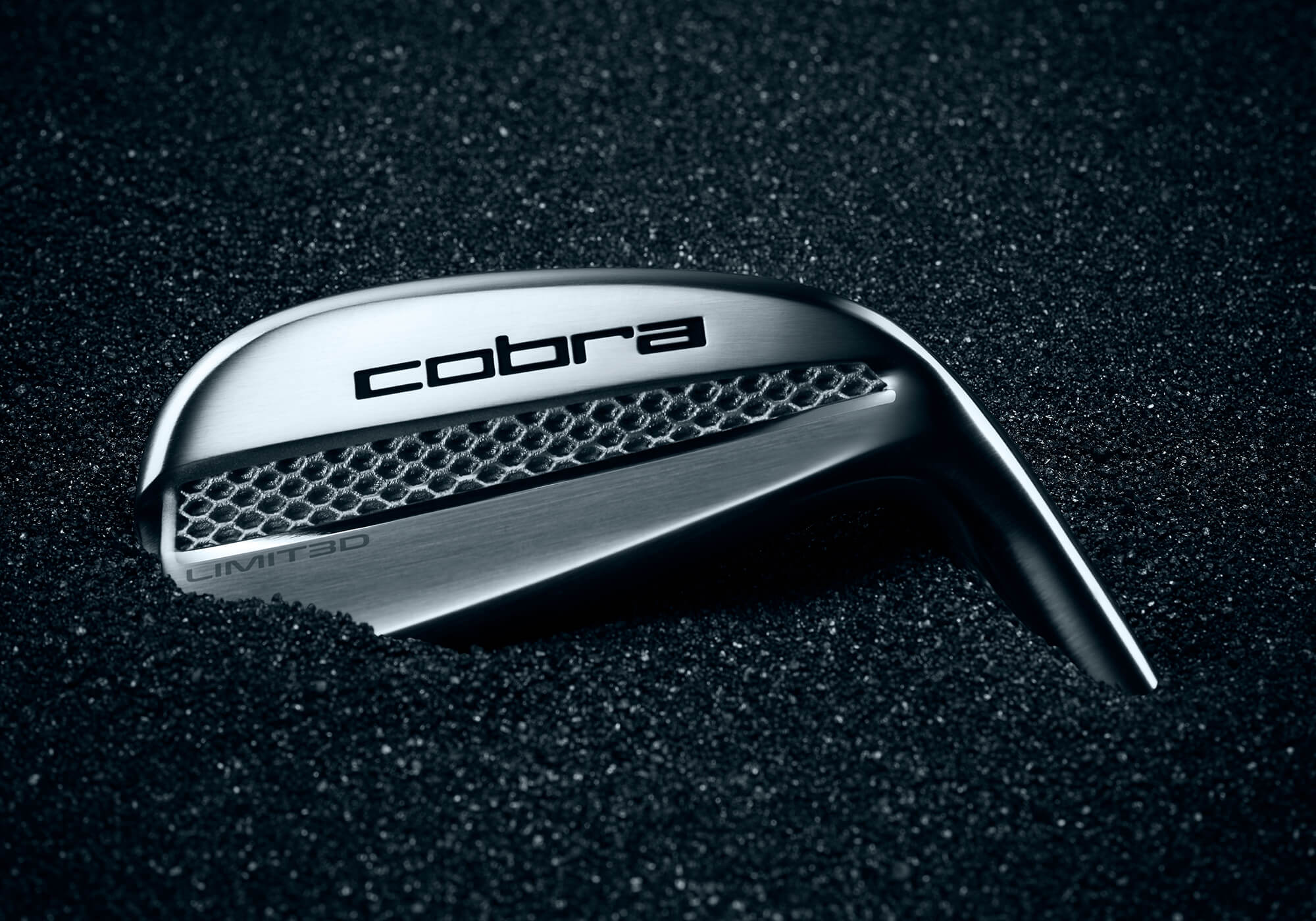
In COBRA’s case, it has been working on 3D printed irons for the last half dozen years. While it has kept its cards close to its vest, COBRA has had 3D printed clubs on the PGA Tour for years.
Rickie Fowler and Gary Woodland have played 3D printed COBRA clubs.
When Kyle Berkshire cracked the face of his conventionally made utility iron, COBRA 3D printed a new one.
That should resolve any questions you might have about the durability of 3D printed irons.
And what about Bryson?
He played COBRA 3D printed utility irons since 2017. He also played 3D printed versions of KING TOUR irons. One might surmise that his previous experience with COBRA is what led him down the 3D printing path with his newest irons.
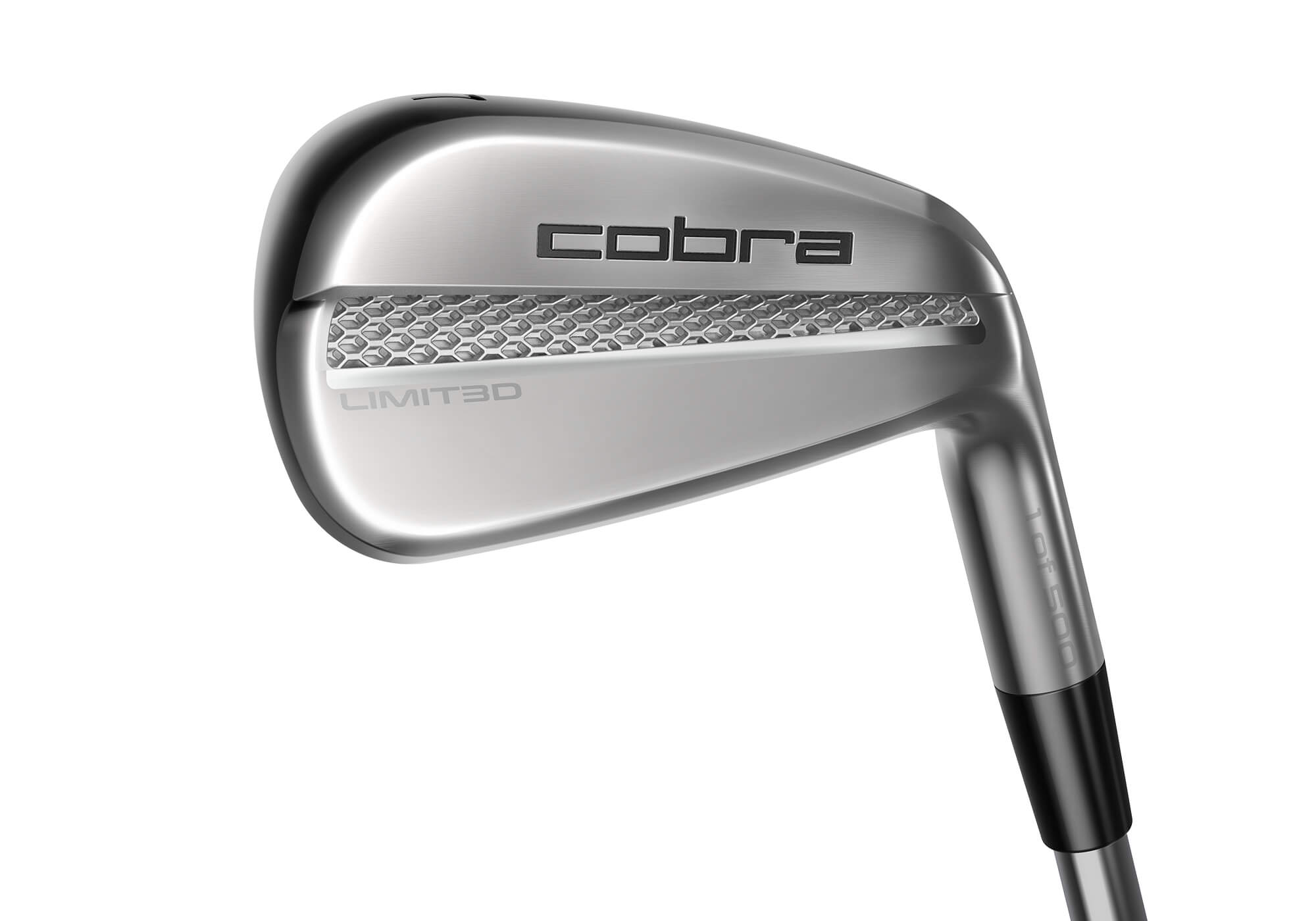
Cool story, but why is COBRA doing this?
The short and simple answer is because it can.
I will shout with my dying breath about how COBRA has never gotten the credit it deserves as one of the game’s great innovators.
To an extent, that’s a necessity of its size but, nevertheless, the company has seldom been content to do things like everyone else.
Where’s the fun in that?
3D printing benefits
What are the benefits of 3D printing? (You may have asked.)
In a word, performance.
It’s not that COBRA LIMIT3D irons will perform like no iron has before. You’re not going to get 10 more yards and you’re not going to rattle every flagstick from 150 yards but they do bring us closer to what is often regarded as the Holy Grail of iron design.
It’s not lost on me that some of you prefer the look of a solid game-improvement shovels but the majority of us drool at even the possibility of an iron that offers the forgiveness of a game-improvement iron with the compact design footprint of a player’s iron.
That’s what you’re getting with the COBRA LIMIT3D iron.
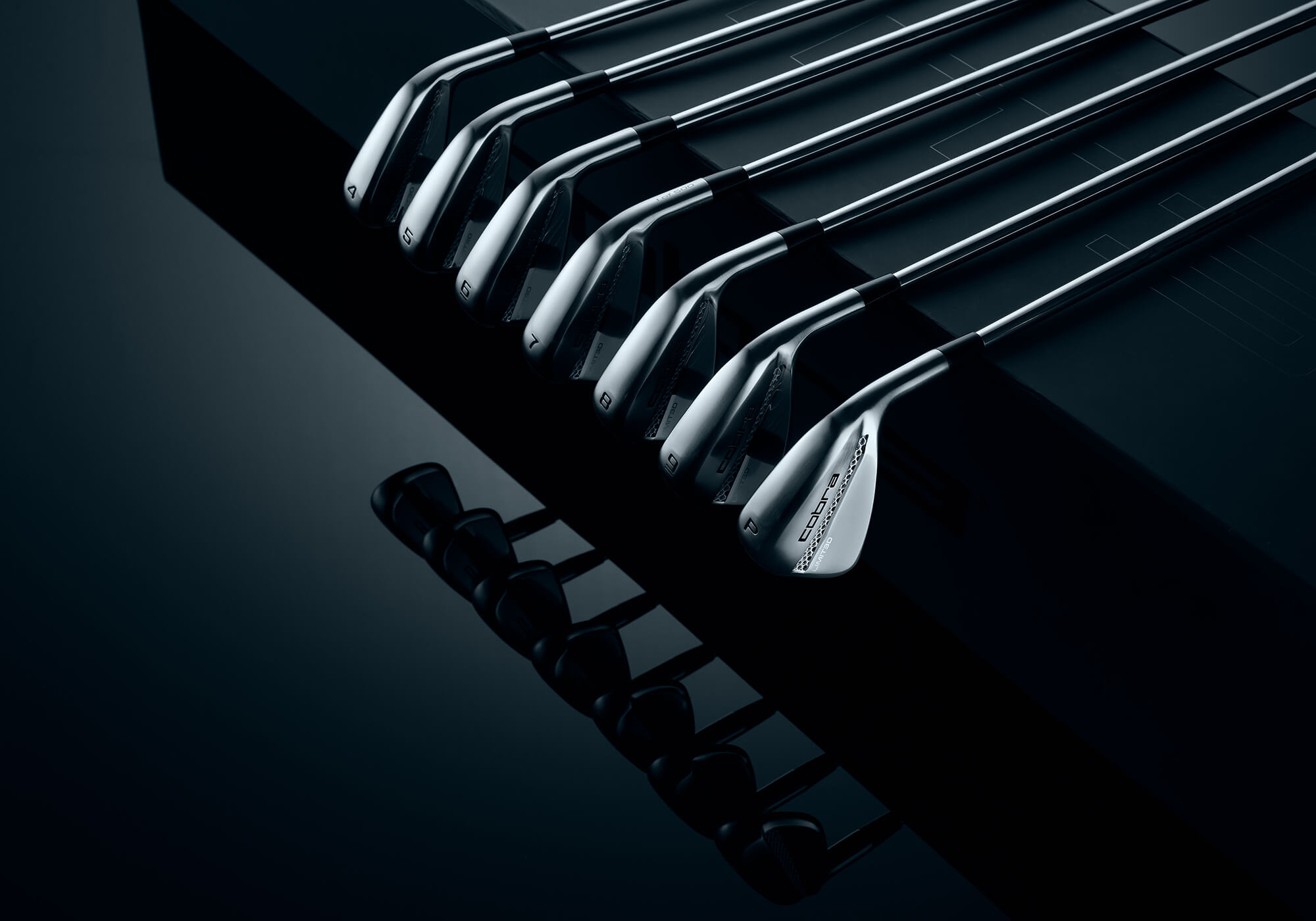
And for sure, COBRA isn’t the first to claim game-improvement performance from an iron that looks like a blade. At times, there has been a hint of truth in that but really what we’re talking about are clubs that hid their size via design tricks. Those work to make an iron look smaller than it is but it’s bigger than a blade just the same.
You get the clean lines,but not the true player’s shape. There’s always been a sacrifice: size, feel … often both.
What separates COBRA’s LIMIT3D irons from the pack is that it delivers on the promise of forgiveness from a player’s shape. It’s not technically a blade but the LIMIT3D are more compact than COBRA’s KING TOUR irons.
We’re talking about decoupling form and function and, in that respect, this might be the rare blade (or something like a blade) that will make you a better ball striker.
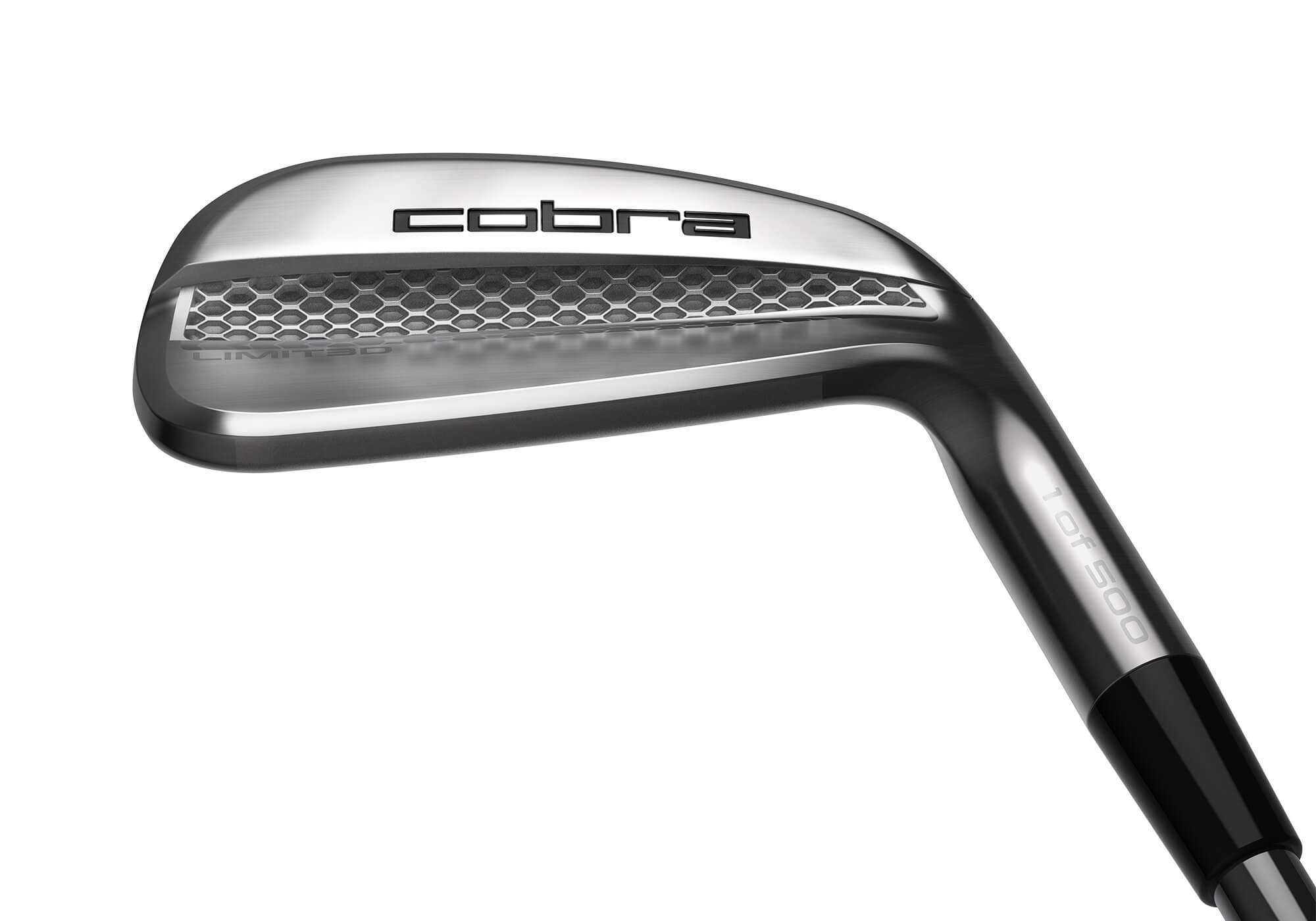
How COBRA LIMIT3D irons are made
COBRA’s 3D printing method might make Rumpelstiltskin proud. It’s not exactly straw into gold but the process that turns 316L stainless steel powder into a golf clubhead feels like one of those things that shouldn’t be possible.
Full disclosure: I’d say the same thing about a camera. I mean, I look at something, click a button and then that thing I was looking at is captured forever. How does that work?
I feel the same way about using laser beams to fuse powdered metal into the shape of a golf club.
At this point, if you said sorcery was the only explanation, I’d be fine with it.
A single iron head consists of approximately 2,600 layers. The machines that form the irons are capable of printing 20 heads in 24 hours.
A quick aside: This isn’t the same process COBRA uses to make its 3D putters. It’s not a case of one method being better or worse than the other. It’s just different and COBRA chose the method most appropriate for task.
While a compact but highly forgiving golf club is the result, the reason it’s possible (other than sorcery) is that 3D printing allows designers to create geometries that are far more complex than what’s achievable with forging, casting or milling.
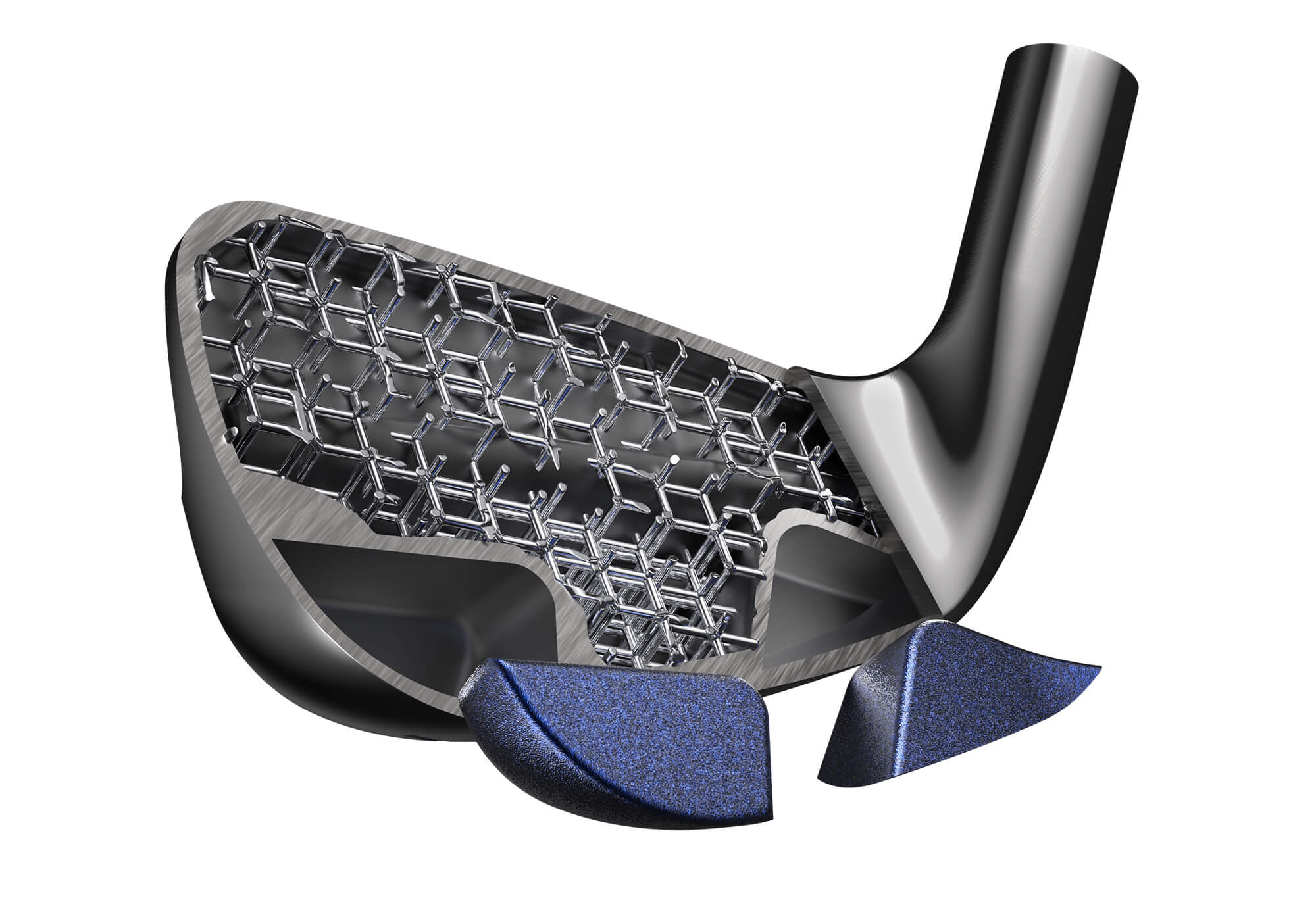
In the case of the LIMIT3D iron, the backside of the face is comprised of a dodecahedral lattice pattern that provides the structural integrity necessary to support the face while saving a metric shit-ton (that’s a technical term) of weight.
FYI: The lattice pattern visible in the back cavity isn’t part of the structure. It’s a visual cue that serves to help tell the tech story.
In a typical solid construction, the face piece or core of the club weighs between 100 and 122 grams. COBRA’s latticed core weighs just nine to 12 grams depending on the loft.
Do the math, guys. We’re talking about massive savings.
How did COBRA reallocate that mass?
You know the answer. They used big chunks of tungsten in the heel and toe (a total of 70 to 100 grams depending on the loft) to drive the center of gravity lower and MOI numbers higher than any iron in their lineup.
When the dust or, I suppose, the 316L steel powder settles, what’s left with is a golf club with a true player’s iron shape and forgiveness that surpasses game-improvement designs.
Said another way: more speed, higher launch and more forgiveness in an eye-pleasing package.
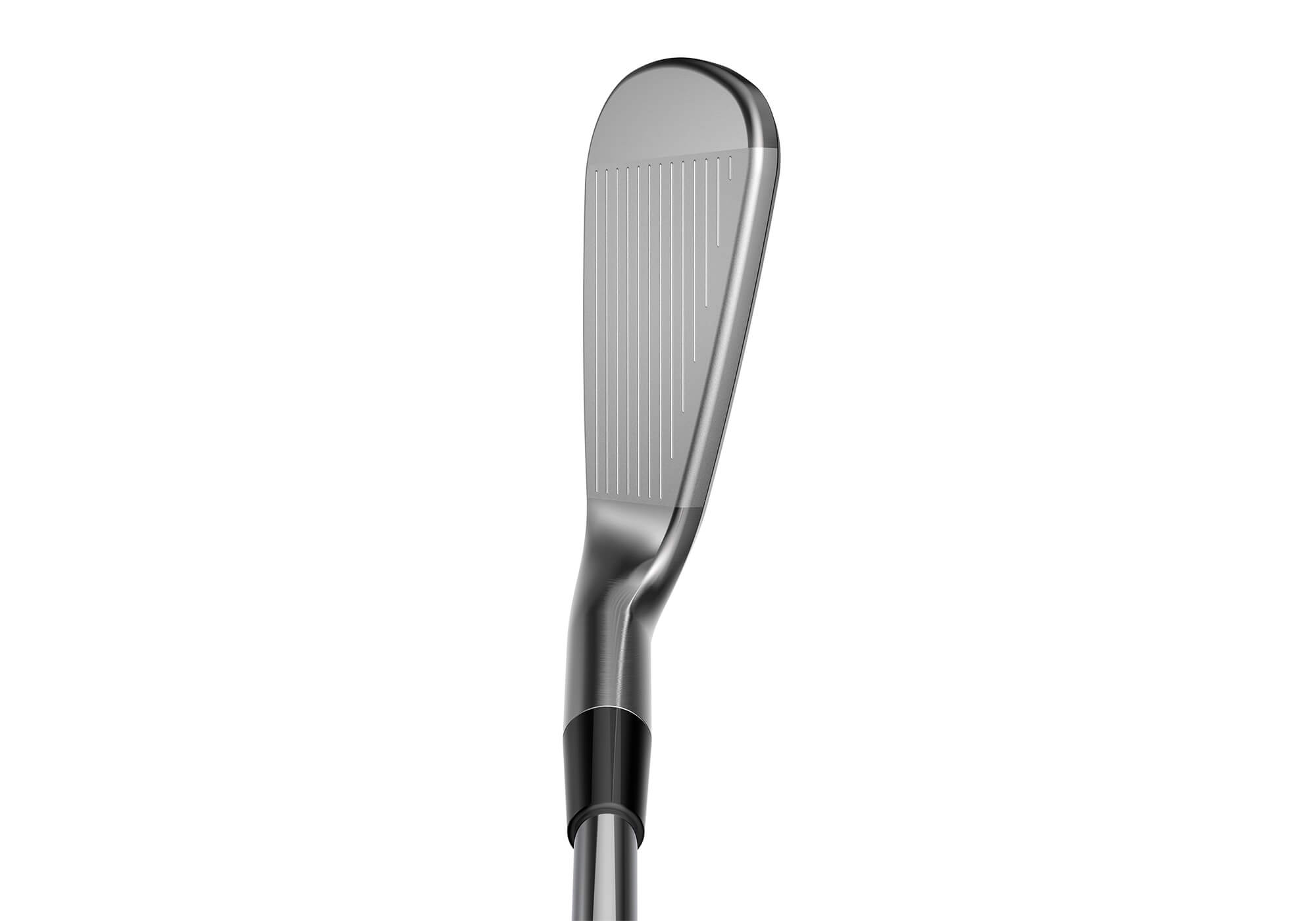
COBRA LIMIT3D Performance
In robot testing versus the KING TOUR, COBRA saw nearly 2 mph more ball speed and an additional five yards of distance with a 7-iron.
The LIMIT3D is a degree stronger but the shaft is a tick shorter. Some of its speed is coming from loft, but not all of it. Expanding testing to include misses, the LIMIT3D is longer still and offers tighter dispersion. So, again, game-improvement performance from a club with a Tour-sized footprint.
What about feel?
On one hand, maybe you shouldn’t care about feel. On the other, it’s no small part of reason why people play player’s irons.
I’ll reserve judgment until I have the chance to hit the LIMIT3D but COBRA’s modal analysis (a means to measure the frequencies of a clubhead as it vibrates and quantify feel) suggests an iron that’s much more similar to muscle-back than something like a player’s distance or game-improvement iron.
Part of the selling point is that the COBRA LIMIT3D don’t just look like a player’s iron, they feel like one, too.
COBRA LIMIT3D irons – How much and how many?
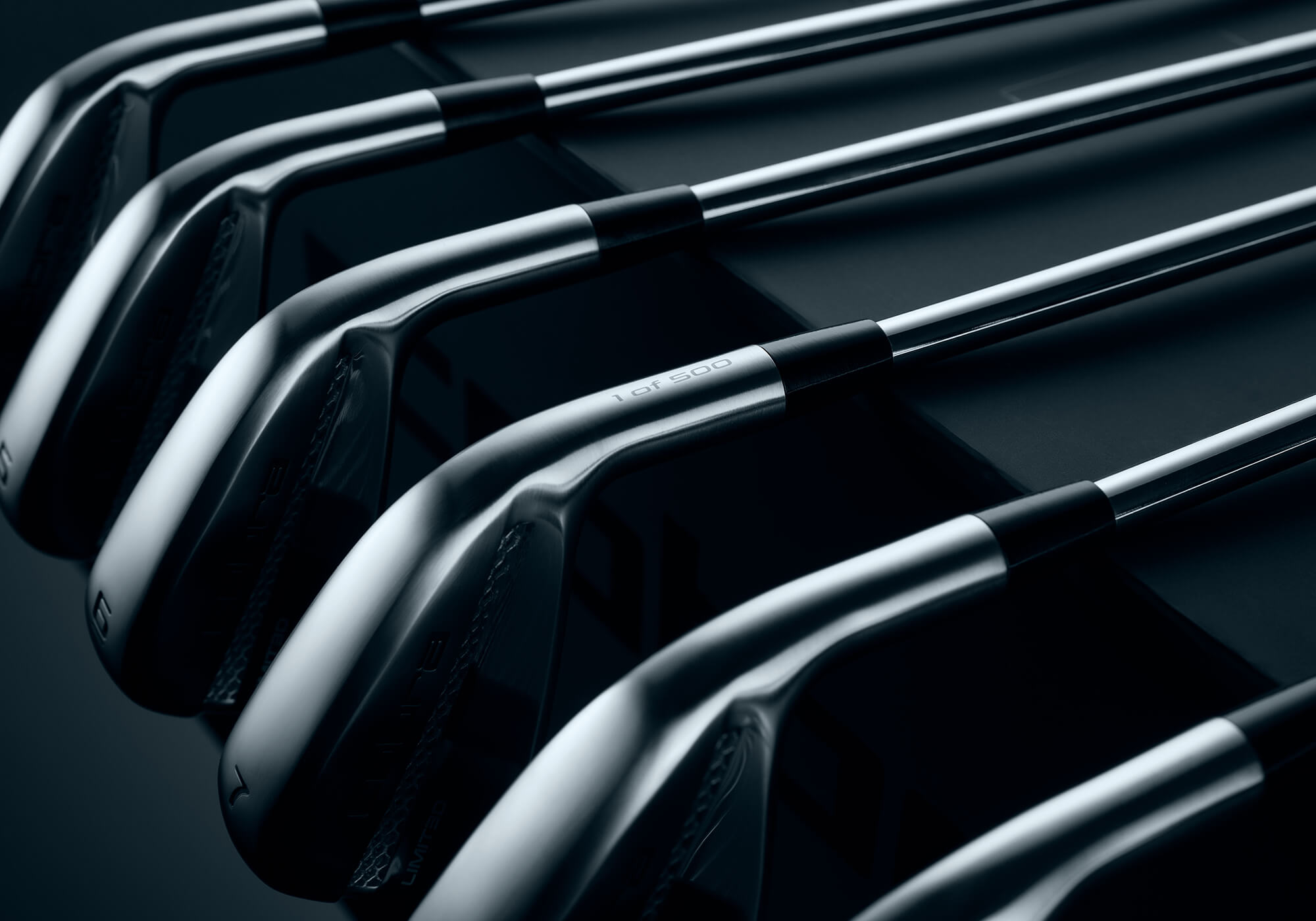
As you’ve been reading along, you may be thinking: These do not sound cheap.
Keen observation, chief. They’re not. It’s not.
But if you do want them, I strongly suggest you bang the Buy Now button the second they go on sale.
Limited is in the name (sort of) and the irons are just that. COBRA has limited production to 500 sets worldwide and only 300 of those will be available in the U.S.A.
Sets will be 4-PW, RH only, and custom only. There is no stock shaft. Each set is built to spec.
The retail price is $2,999.99. Sales begin (and likely end) on June 7.
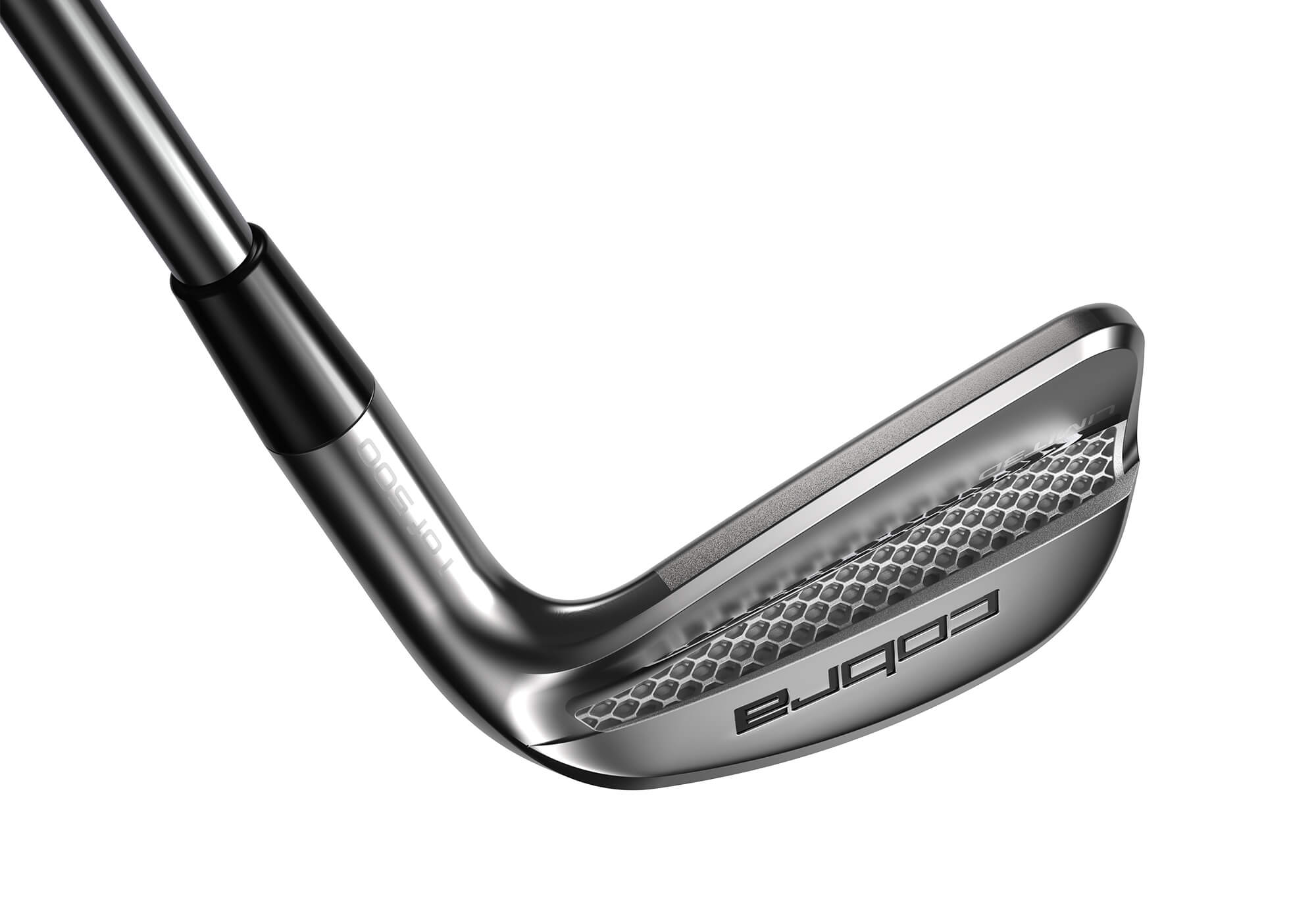
A postscript in all of this: How does 3D printing translate to other categories? 3D printed prototypes exist in every club category but the potential for advancement is likely greatest in the driver category. The requisite size and strength of a driver face means a significant amount of forwardly placed mass is non-negotiable.
Other than the USGA, the face itself is likely the biggest obstacle to innovation.
What if COBRA could achieve the same type of weight savings it did with the LIMIT3D iron in a driver? Would it make for the most meaningful breakthrough since titanium?
I asked COBRA’s VP of Innovation, Mike Yagley, if he wanted to talk about how 3D printing could be leveraged in future driver designs.
“Nope.”
I think what he meant was “not yet.”
For more information on COBRA LIMIT3D 3D Printed Irons, visit Cobragolf.com.
The post COBRA Releases Fully 3D Printed LIMIT3D Irons appeared first on MyGolfSpy.