Golfing News & Blog Articles
The Z-Alloy Story: Has Cleveland Golf Really Developed A Better Wedge Material?
When it comes to all things wedges, most reasonable people can agree that Titleist’s Bob Vokey is the chairman of the board.
Last summer, MyGolfSpy’s Rick Young asked Vokey where he thought the future of wedges would go.
“We’re always looking at new materials,” said Vokey. “But, honestly, nothing has come along yet that can replace 8620 carbon steel. It’s castable, it lasts, you can grind it … We stay with it because it ain’t broke.”
When Boeing Smith, a PhD-level metallurgist who admits to a lifelong Everest-size chip on his shoulder, read that, all he could do was just smile.
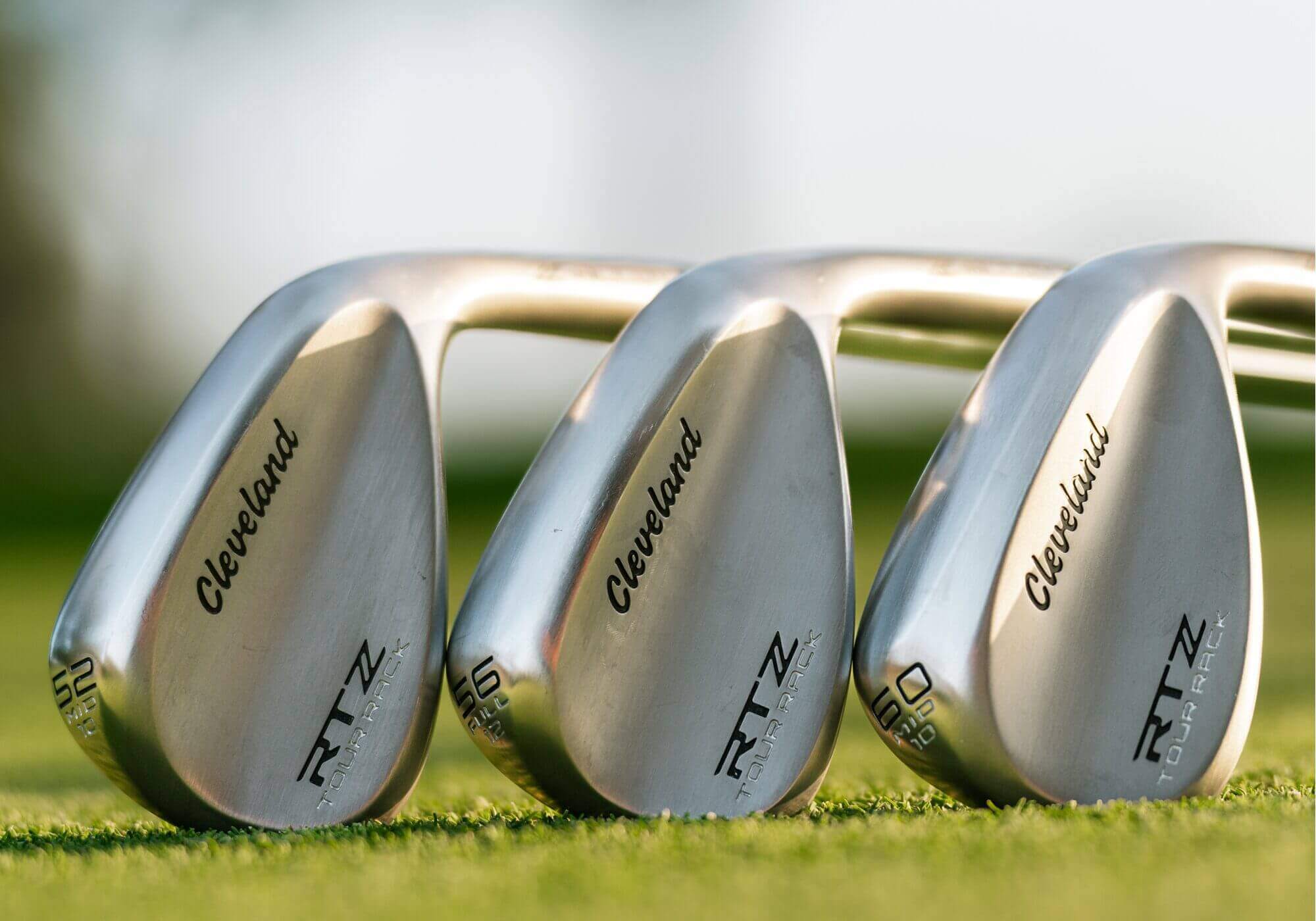
He was, after all, in the process of replacing the irreplaceable and breaking what wasn’t broken.
Smith, you see, works for Cleveland Golf, and he’s the guy behind Cleveland’s all-new wedge material, Z-Alloy.
Trust us. This is a story you want to hear.
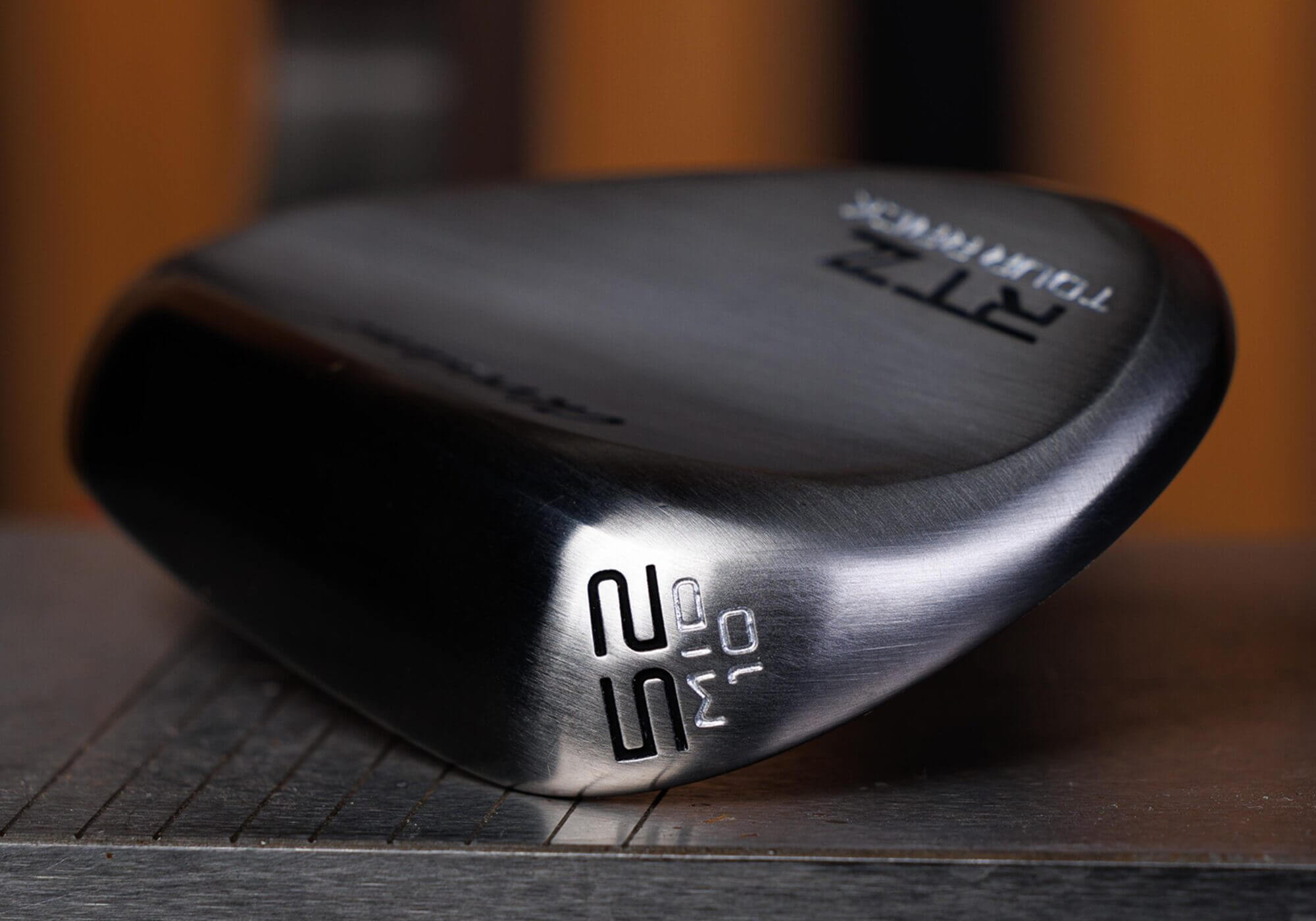
The Zen of Z-Alloy
At 64, most people I meet look like kids but Boeing Smith, at age 31, looks a good bit younger. Don’t let his Opie Taylor demeanor fool you, though. Smith is a senior research engineer at Cleveland with bachelor’s degrees in physics and chemistry along with a master’s and PhD in welding/metallurgical engineering.
His doctoral project involved relating metal hardness, strength and wear resistance to impact resistance which, if you think about it, is kind of important when it comes to golf clubs. Oh, he’s also been as low as a plus-2 handicap.
The dude is straight out of Central Casting.
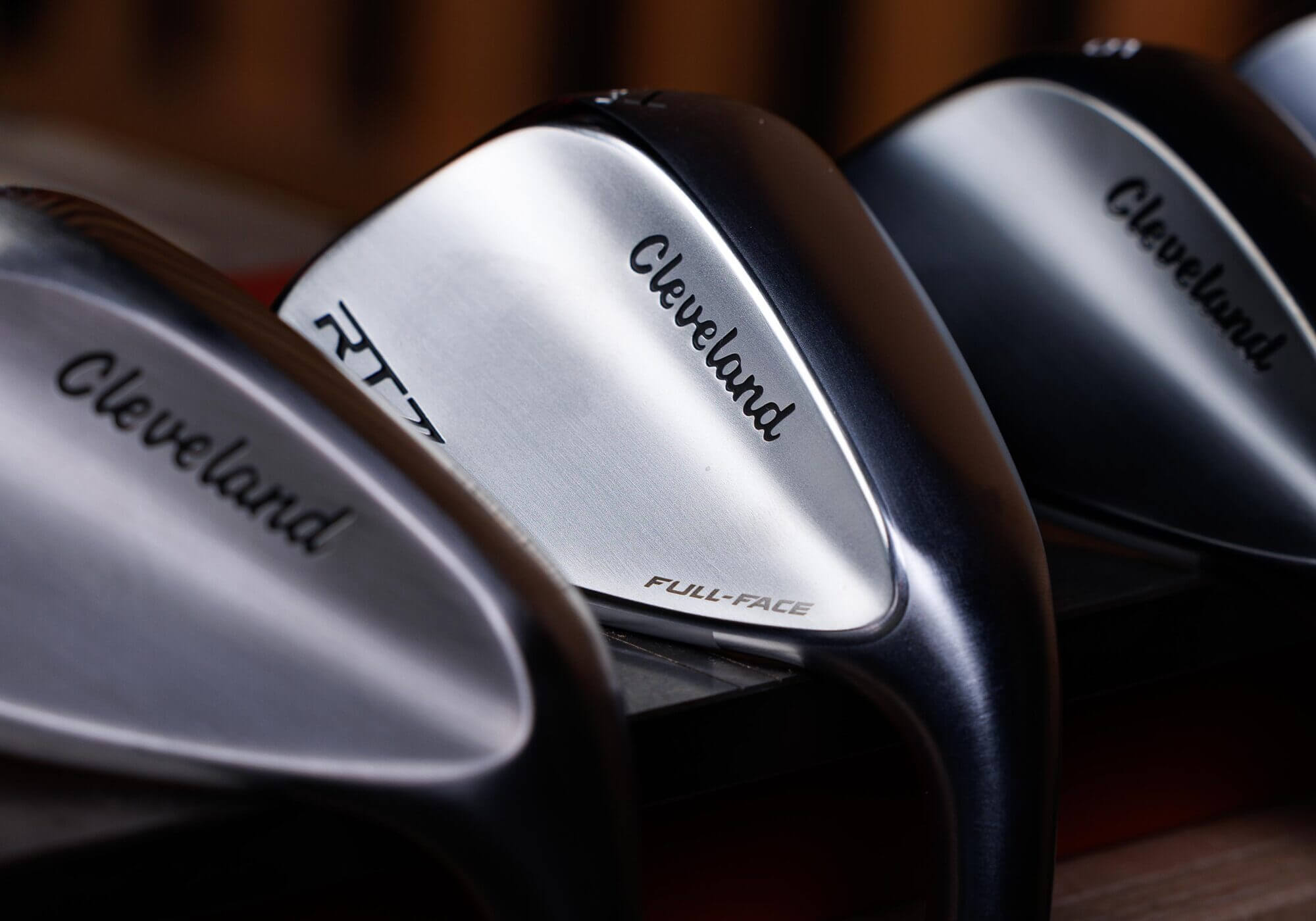
Smith joined Cleveland three years ago and was immediately assigned a very specific task: find a wedge material that’s better than 8620. He met with the engineering, marketing and product development teams, asked a lot of questions and took a lot of notes.
“They asked for things like forgiveness,” Smith tells MyGolfSpy. “But how do you make something more forgiving? You move discretionary weight. That translated to density. They also wanted it to feel really good. That meant the material had to be softer.
“They also wanted it to last a good while. That meant it had to be durable.”
From those meetings, Smith developed criteria and started hunting for a wedge material that could beat 8620.
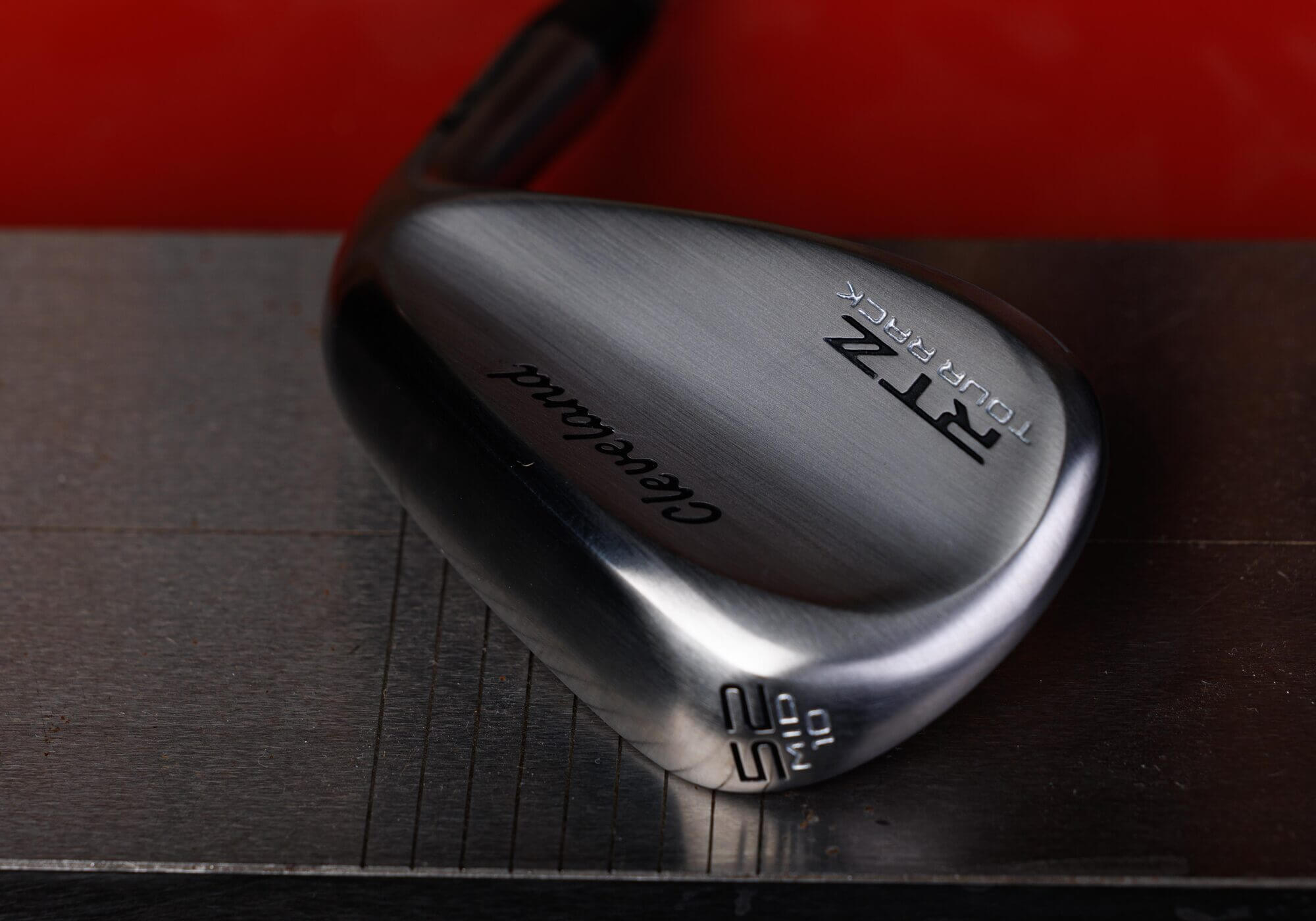
What’s behind Door No. 3?
Smith reported back that he found three materials that might work.
“One of them was from the oil and gas industry. It beat 8620 in like three categories. The second was from aerospace and it beat 8620 in four categories.”
The last material, however, beat 8620 in every category, hands down.
“They asked me, ‘Where’s that one from?’ I said, ‘It doesn’t exist yet. We’ll have to make it.’”
For a kid who grew up on SpongeBob and Hey! Arnold, he doesn’t lack for confidence.
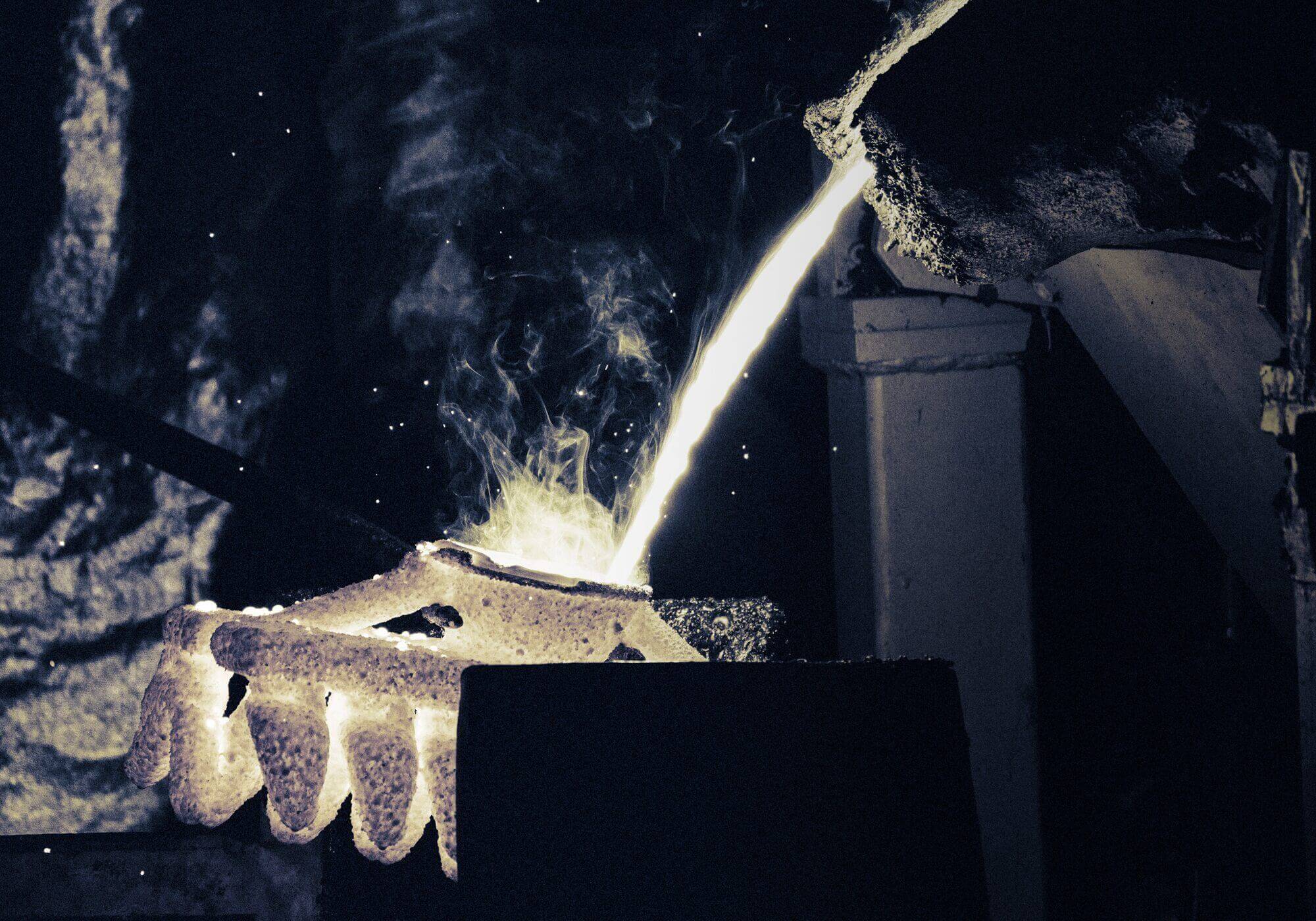
Also, don’t think for a minute that Smith went the artificial intelligence route to develop Z-Alloy. He did it the old-fashioned way. He dug into his textbooks.
“Some of my books look like Harry Potter’s in The Half Blood Prince with all the notes and highlights.”
So how does one go about creating a material that didn’t exist? Again, Smith started by asking questions.
“I asked myself what crashes an airplane and what breaks a pipeline? Does the same thing break a golf club? In some instances, the answer is no. So then can I trade off what crashes an airplane but doesn’t break a golf club to check off every box?”
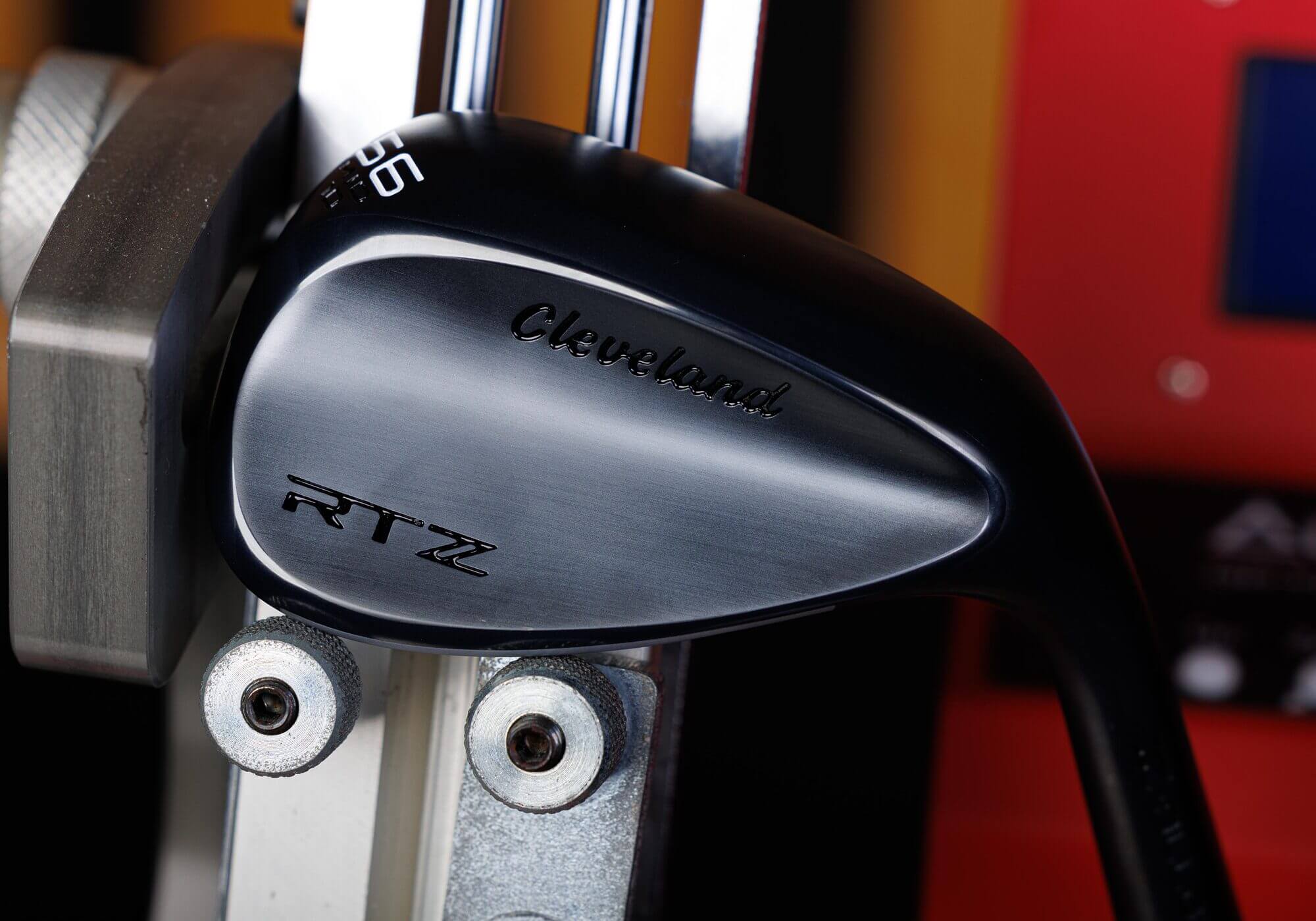
The Z-Alloy alchemy dichotomy
Smith and his team set out to create a material with seemingly incongruous properties. It had to be soft for feel but hard for durability. It also had to be low density to create discretionary weight but also strong enough for casting, grinding and bending.
And rustproof would be nice.
“The chemistry and physics in which you manipulate things like softness and durability aren’t completely mutually exclusive,” he explains. “There were some dials I couldn’t turn too far or else we could mess things up.”
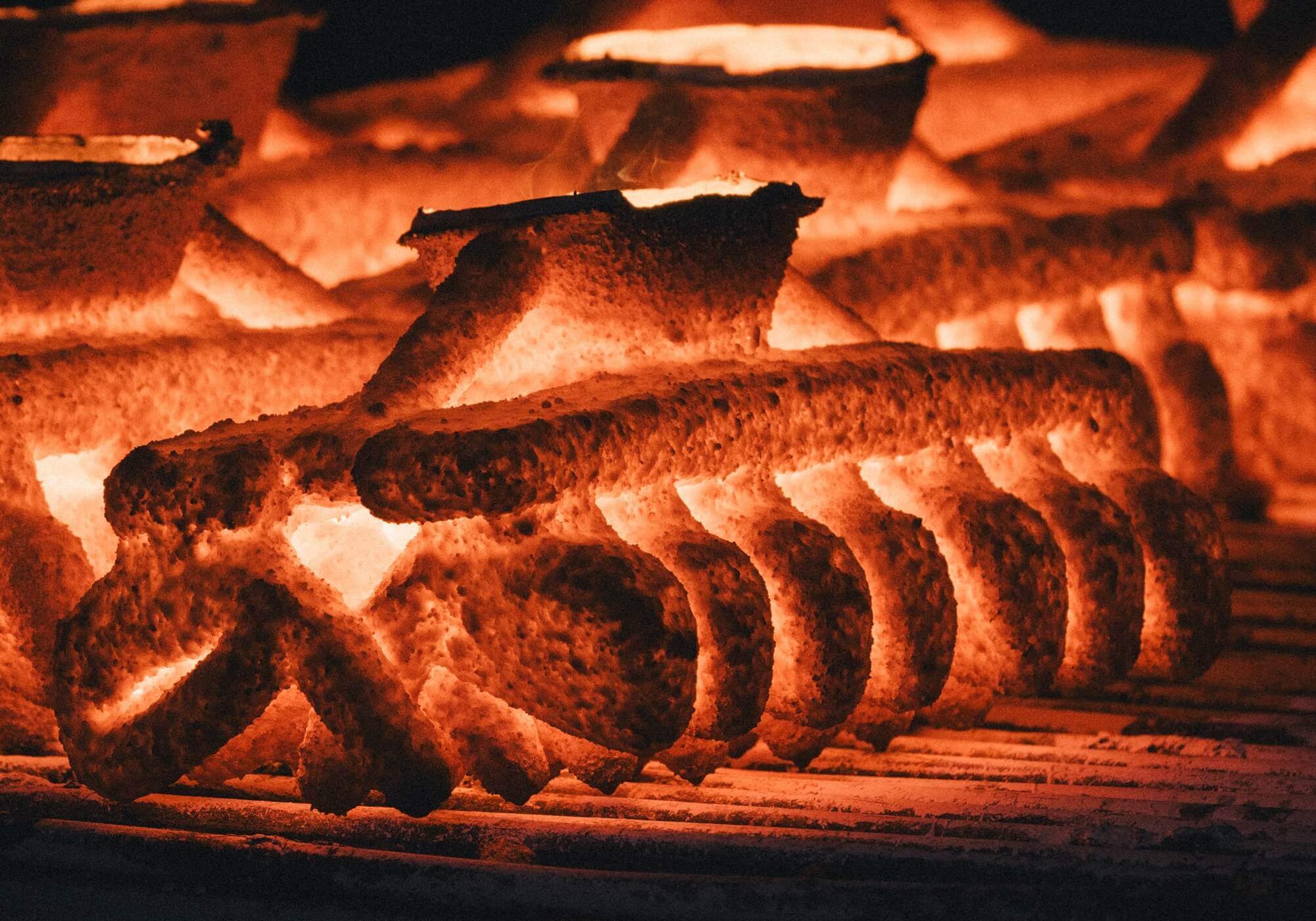
Smith wouldn’t dive too deeply into the metallurgy of it all (the patent is pending) but he did confirm the lower density of the material saved about six grams worth of discretionary weight. In golf club design, new discretionary weight always comes with a tradeoff so when the wedge design team asked what they’d have to give up to get those six grams, Smith smiled and said, “Nothing. It’s free. Move it wherever you want.”
Z-Alloy’s rustproof properties also relate to durability. We’ve said it so many times already but once more won’t hurt. Rust doesn’t add spin. Raw, un-plated wedge faces may enhance spin. It all depends on who’s making it.
Rust is corrosion and corrosion is bad for wear resistance.
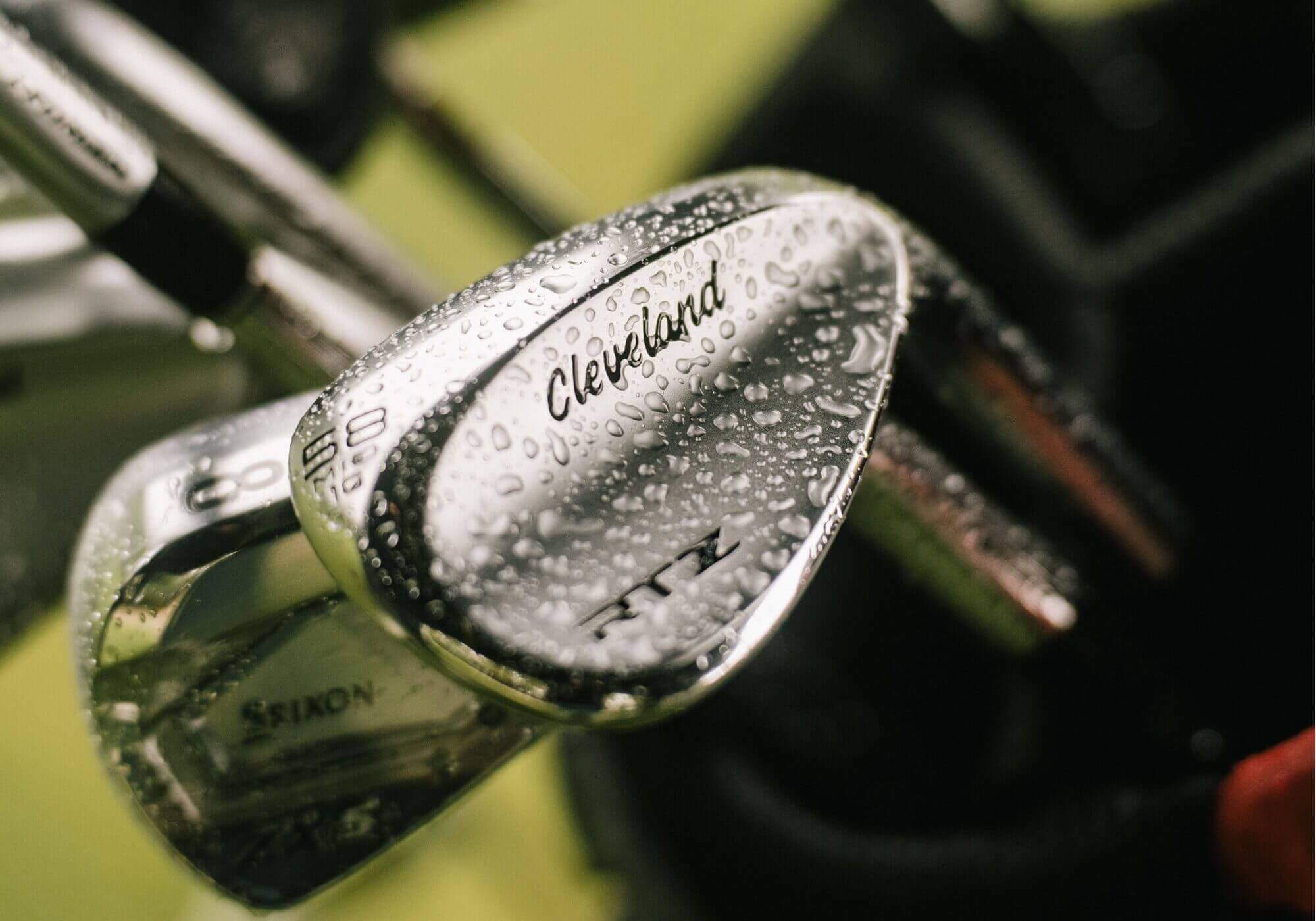
“Carbon can control some properties in steel,” he says. “I dialed that to where I could control density and wear resistance. I dialed in other elements separately while knowing how high I could go to where they wouldn’t be catastrophic when we put them together.”
Durability and the 87-percent solution
Soft and durable?
Yep, that’s what Cleveland is saying. Despite feeling softer than 8620, Smith turned enough dials to also make Z-Alloy more durable when it comes to groove wear. Once prototypes were made, his team did some side-by-side player testing with Cleveland’s previous generation raw 8620 wedges.
“We did the test with three Z-Alloy wedges and three 8620 wedges. These were done on the course with real players hitting all kinds of shots. We took groove scans before and after and groove wear was 87-percent higher with the 8620 wedges.
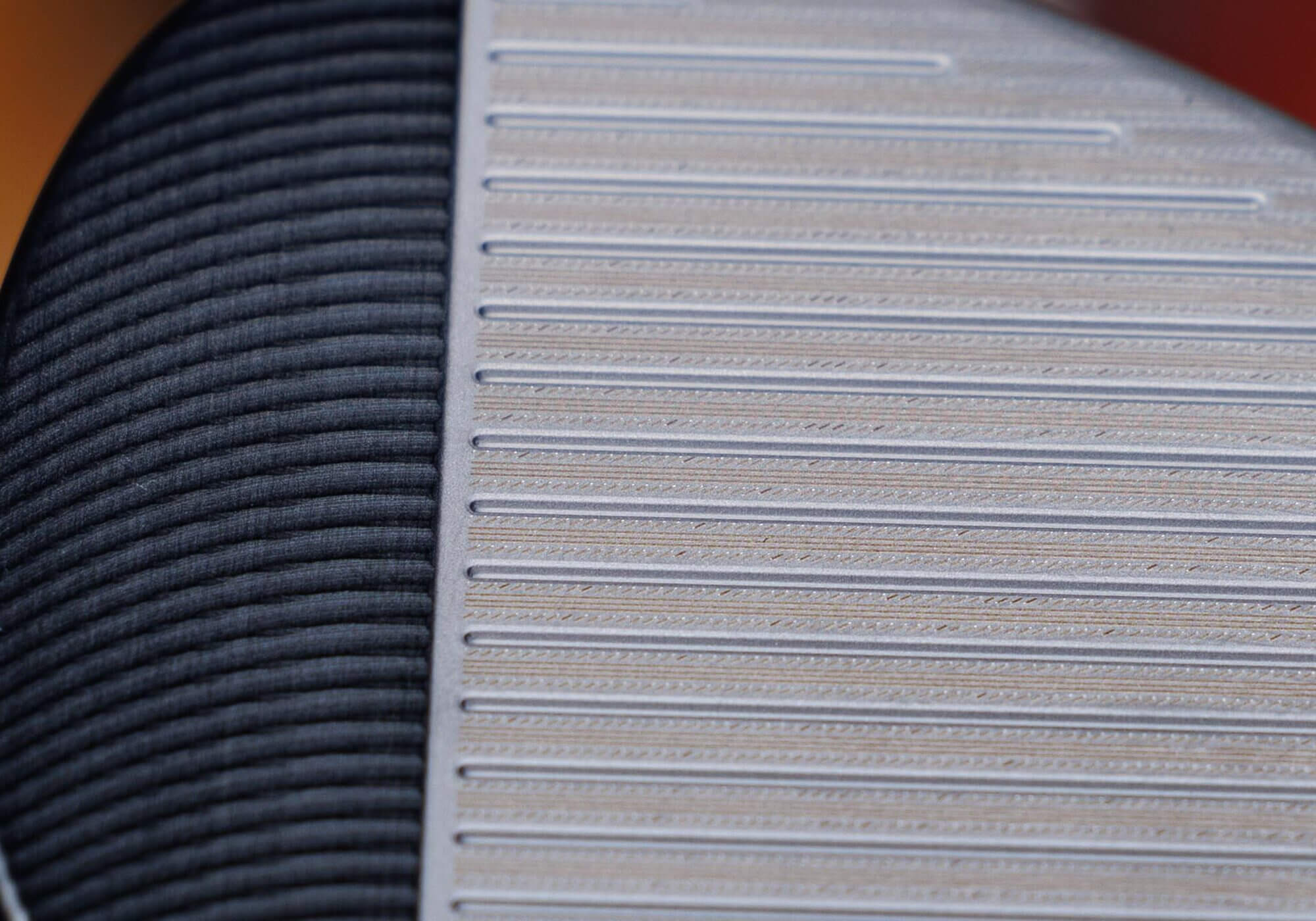
“The results were pretty astounding but the Research Department said, ‘We don’t believe you. Go out and do it again.’ We did and we got the exact same results.”
Cleveland says its pro tour staff adopted the RTZ wedges faster than any other new product in recent memory. As for wear, Brooks Koepka normally replaces his lob wedge every month. His first RTZ stayed in the bag for over two months.
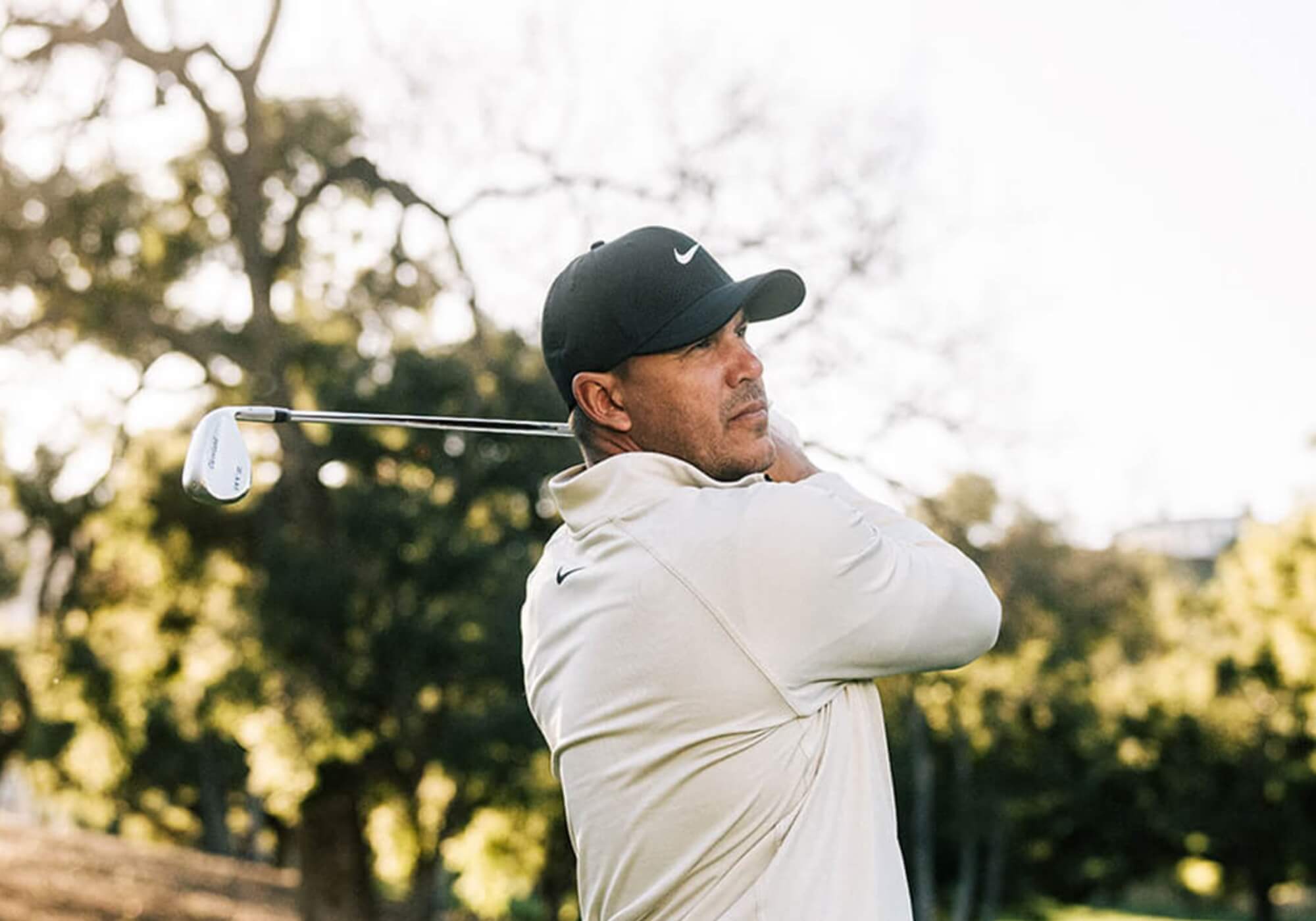
The journey to Z-Alloy wasn’t always smooth
It’s important to reiterate that Z-Alloy is a truly new material. It’s not that it just hasn’t been used in golf before. It hasn’t been used ever before, anywhere.
At least on this planet.
“This isn’t military grade and it isn’t aerospace grade,” says Smith. “It’s golf grade. I’d never put this material in an airplane or a pipeline. I would definitely put this in a golf club.”
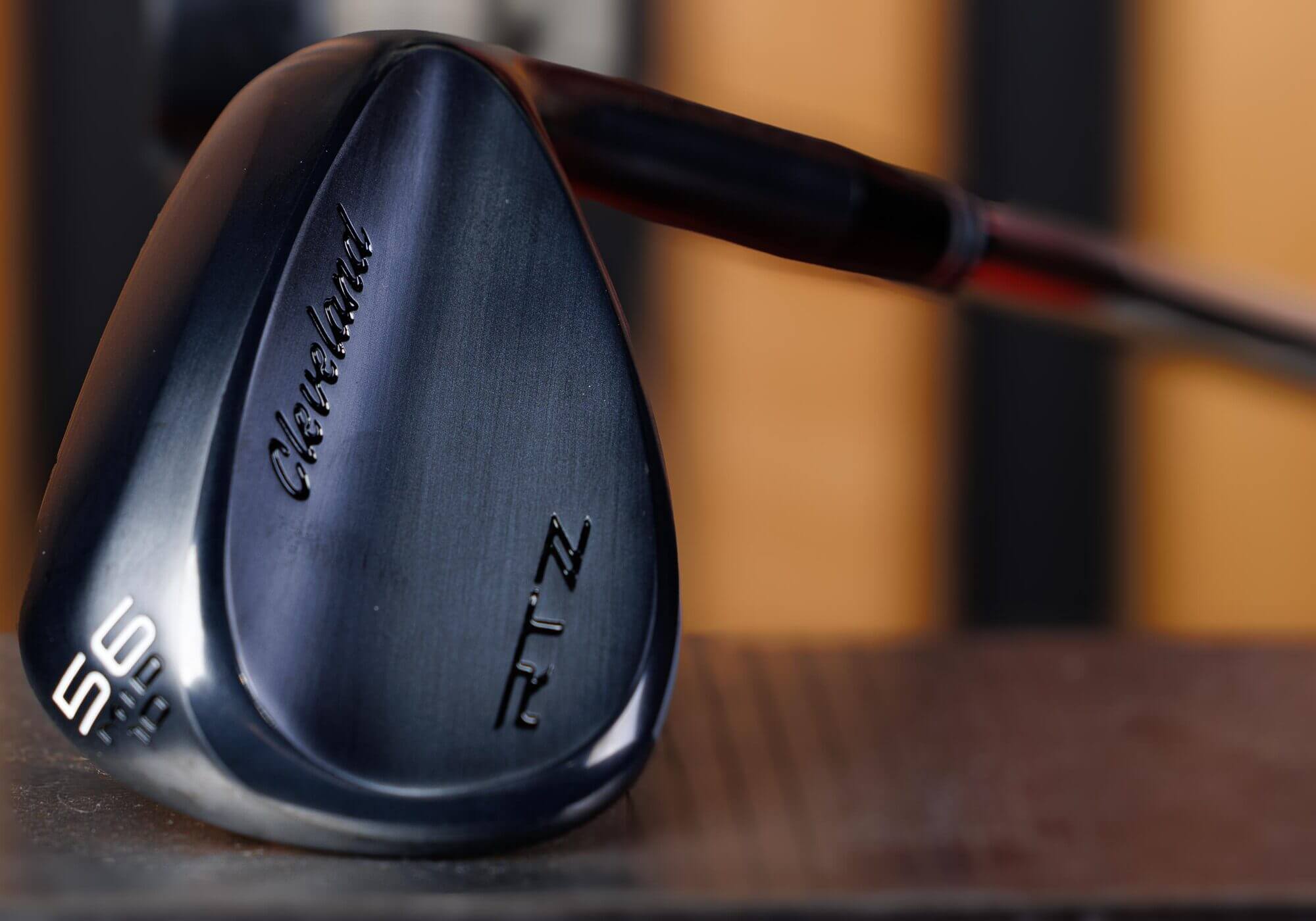
From start to finish, Smith estimates the project took a good three years, most of that spent working 60 hours a week. He got the material right fairly early on with help from Cleveland engineers Rick Fillon and Jake Grenier but the road to prime time was a little bumpier.
“There were times when we wondered if we should pull the plug on all this. Whenever you make a new material, you’re kind of venturing into the abyss. You have to be prepared for something new to pop up.”
While the material itself is unique, don’t expect it to find its way into Cleveland irons. Z-Alloy was optimized for wedges only.
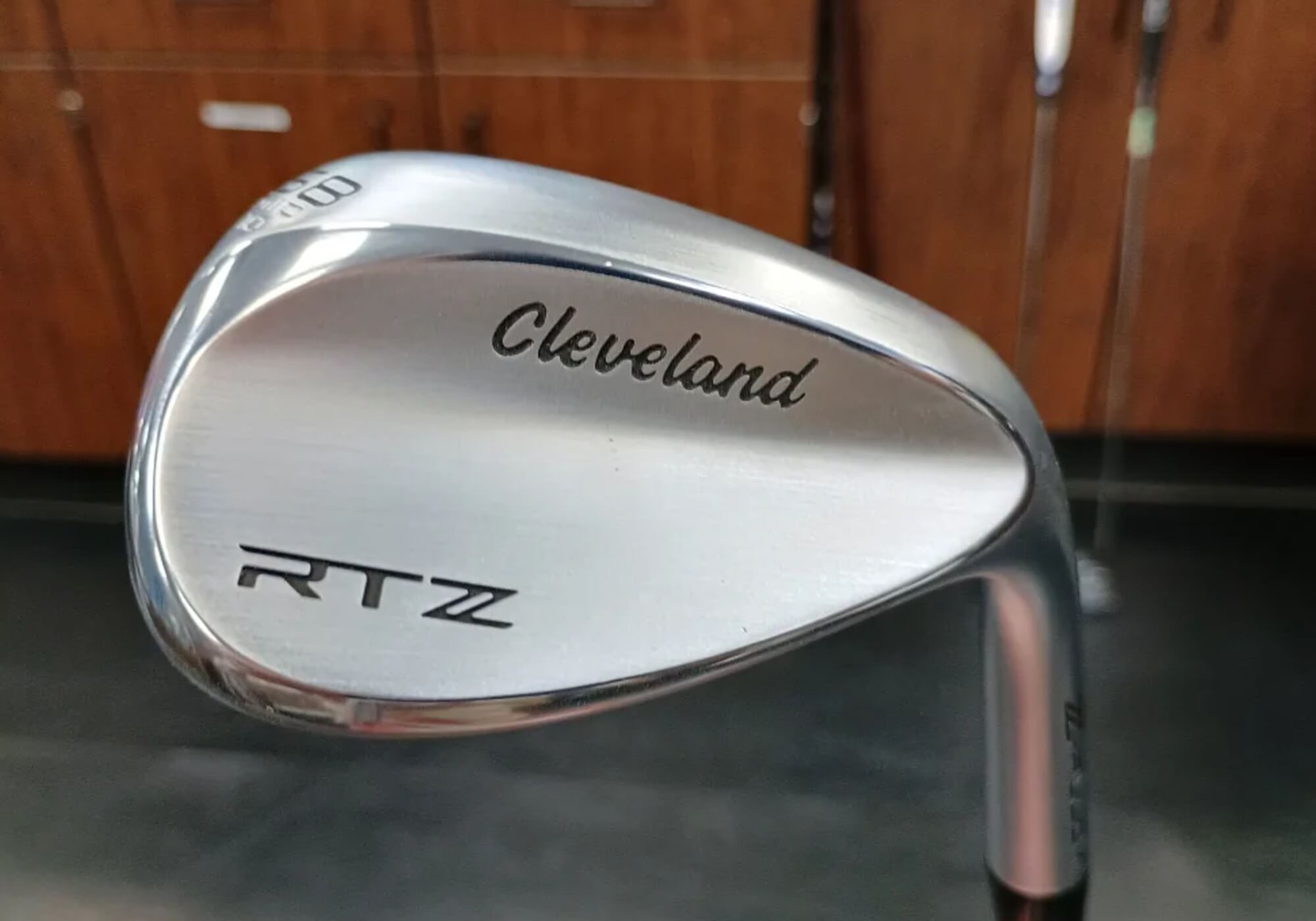
“We traded a lot of other things off,” explains Smith. “It’s not like we just pour this chemistry together and a magical material comes out. We made the formula so we can process it specifically for wedges.”
Smart is as smart does
Despite degrees in physics and chemistry and a master’s and a PhD in welding engineering and metallurgy, Smith doesn’t consider himself a “smart” guy.
“My brother is actually the smart one in the family. There are truly smart people in this world and then there are brilliantly lazy people who appear smart. That’s me.”
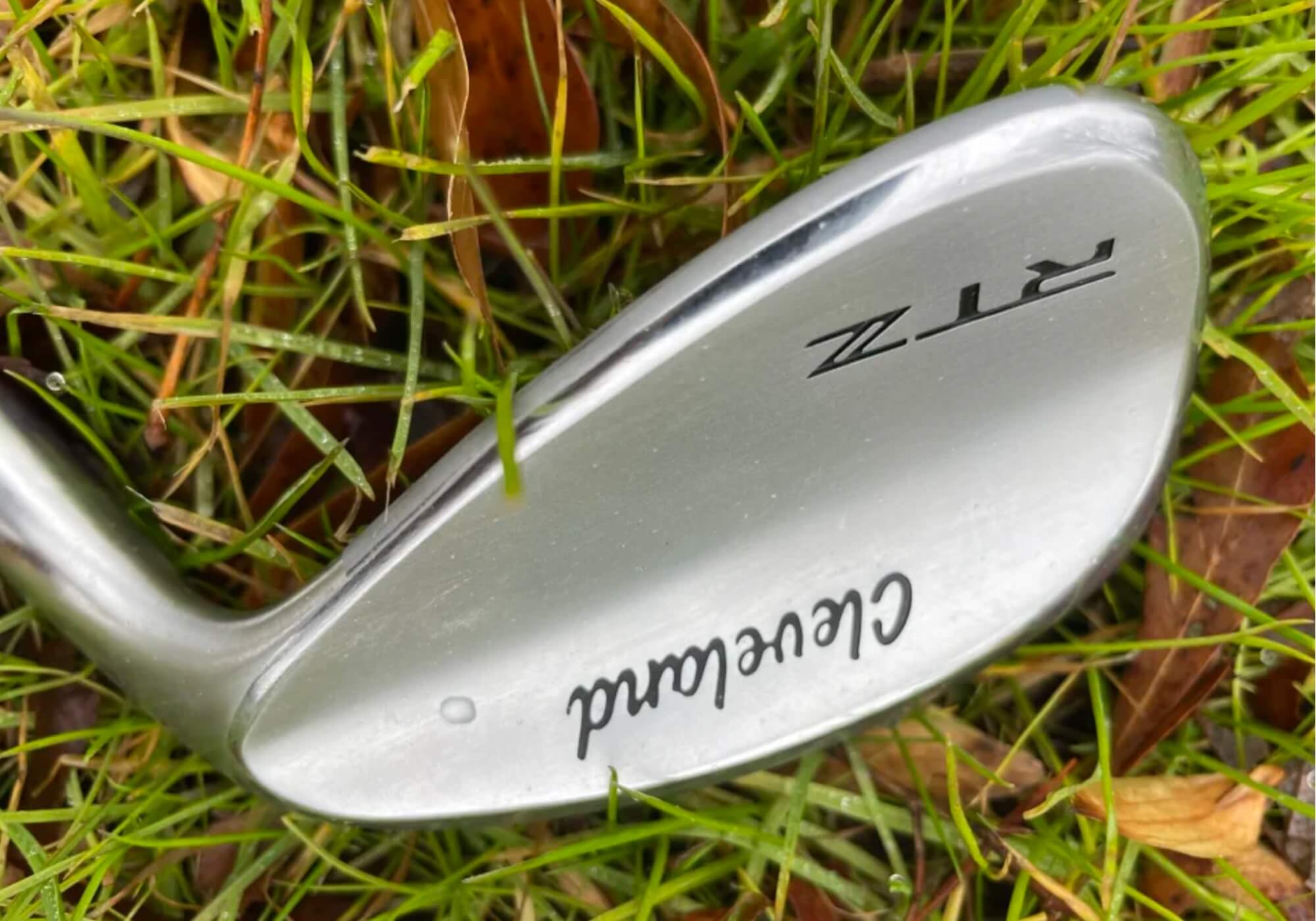
Smith earned his PhD at Ohio State, home to one of only two welding engineering programs in the world (the other is in Japan). He solved his PhD problem in only three years as opposed to the five considered normal.
His professor was not pleased.
“The problem was I solved it in way too simple of a way. I found the measure of what we needed to measure but my professor said I wasn’t advancing the field of science. This wasn’t PhD-caliber work.”
Academia may be all about the process but the real world wants results. It doesn’t care how you find the answer, only that you find the answer.
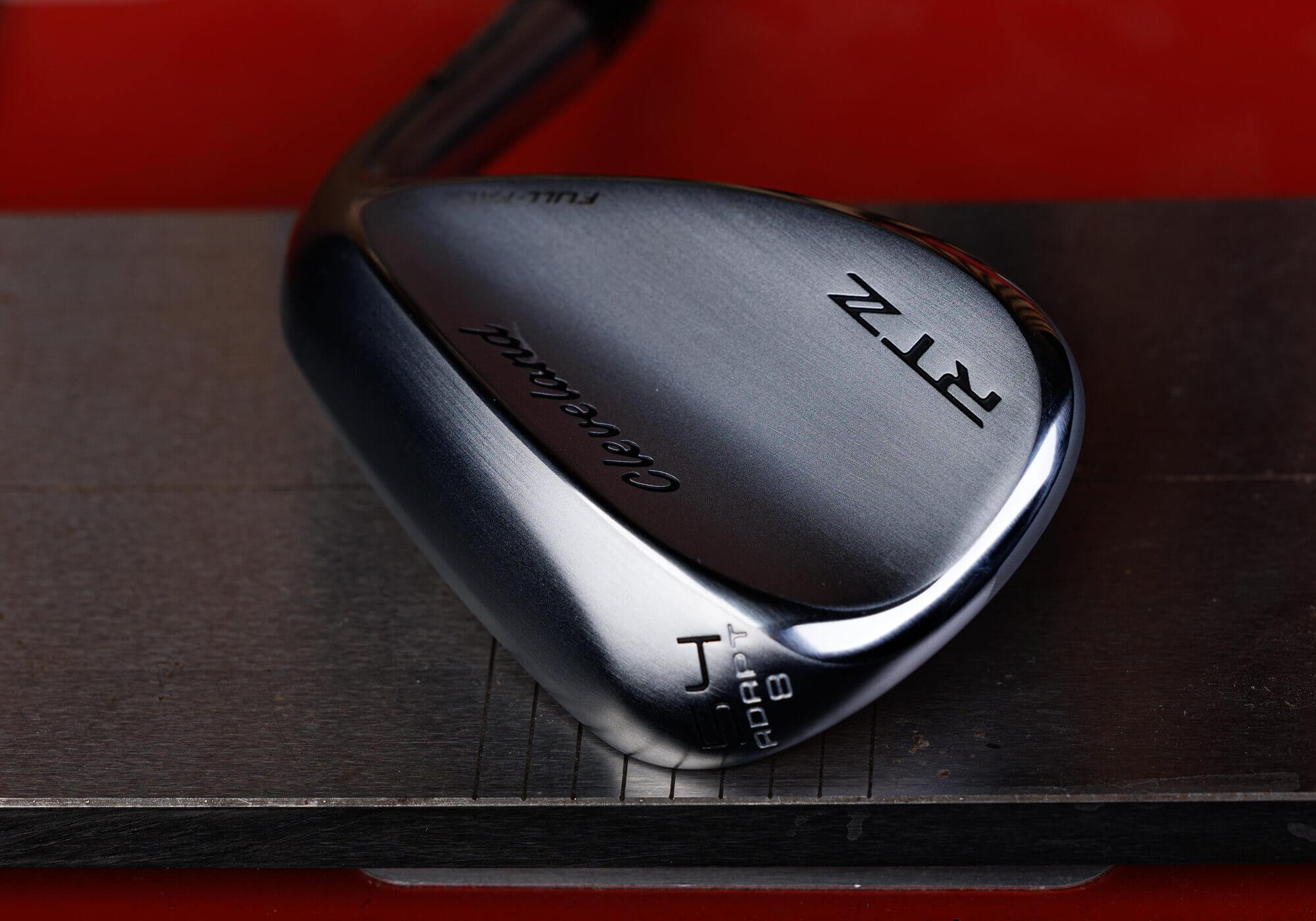
“It’s like that famous Bill Gates quote: ‘I give my hardest jobs to my laziest people. They’ll find the easiest way to solve the problem.’”
About that Boeing thing …
As we neared the end of our conversation, I had to ask about Smith’s first name. After all, he’s the first person I’ve ever met named Boeing.
“My dad’s name was David Smith and he grew up on every bad check list in the world. He said, ‘If my kids have good credit or bad credit, everyone’s going to know it.’ He was into aviation so that’s why my name is Boeing. My brother’s name is Hubble.”

Smith grew up in the small town of Galipolis, Ohio (pop. 3,413) on the Ohio River near the West Virginia and Kentucky borders. He says it’s one of the poorer areas of the country which in part accounts for that large chip he carries on his shoulder.
During his first class as a college freshman at Whittenburg University, the professor asked everyone to introduce themselves and say where they’re from.
“I said, ‘I’m from Galipolis, Ohio.’ This person turned to me later and said, ‘Good luck. The math tutoring center is on the first floor.’ I already had a chip on my shoulder. Thanks for making it bigger.”
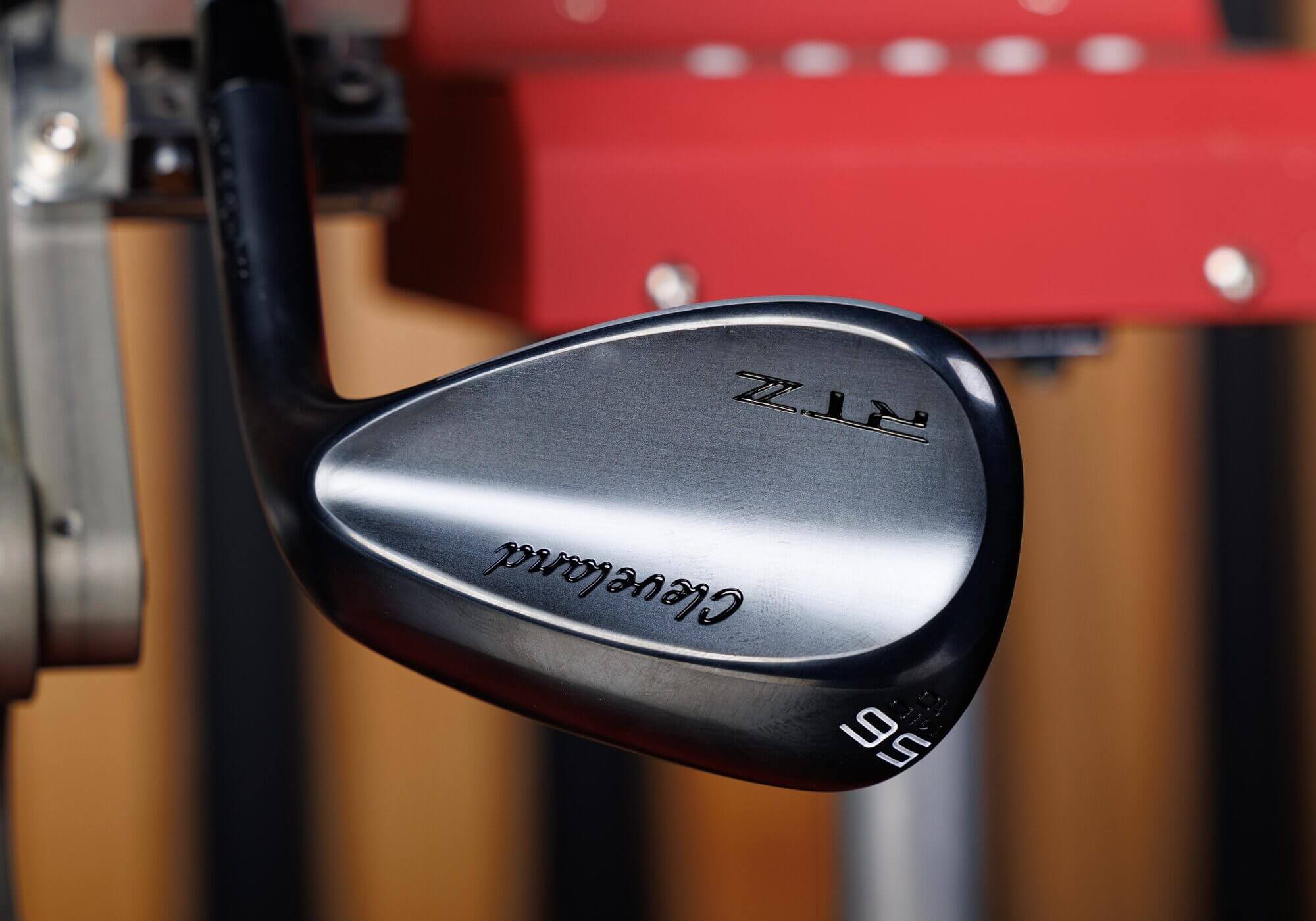
Boeing also became an undergraduate legend when he catalogued the local liquor store by the amount of alcohol per dollar.
“You don’t have much discretionary spending money in college. It’s a very simple formula. It’s proof times volume divided by dollar.”
Solving a problem we didn’t know we had
Creating a wedge material better than 8620 carbon steel probably isn’t on anyone’s 2025 bingo card. As Bob Vokey said, it isn’t broken, so what’s the point?
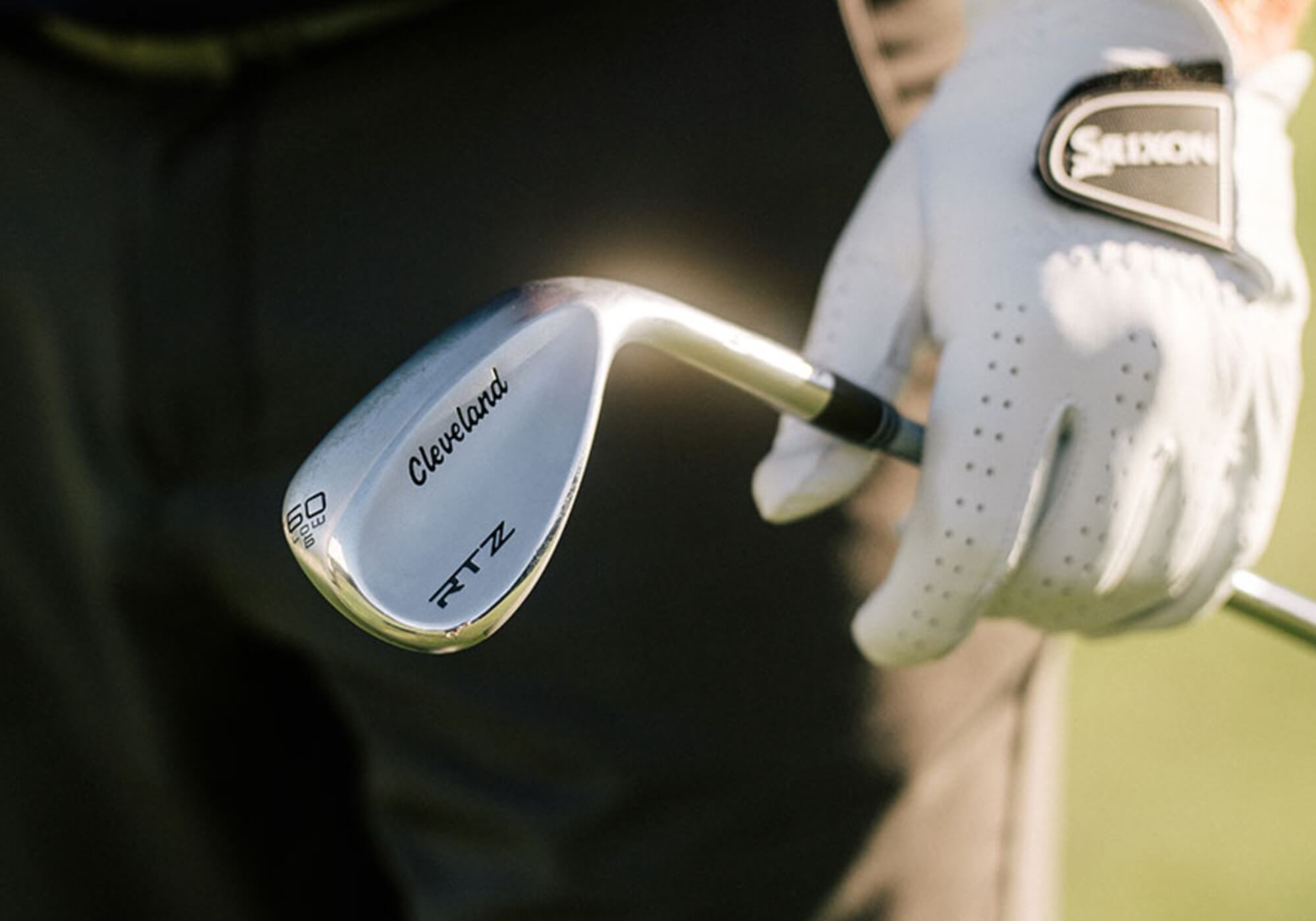
There are two answers to that question. For Smith, it was simply a problem he was given to solve. As a metallurgist, he didn’t worry about whether it was financially viable or even necessary. His goal was to find a material that would be softer and more durable than 8620 and wouldn’t rust.
For Cleveland, it’s a bigger question and a bigger risk. Why change something if it works just fine? With Vokey the runaway market leader, Cleveland continues to duke it out with Callaway and TaylorMade. However, the old axiom says if you keep doing what you’ve been doing, you’ll keep getting what you’ve been getting. If you’re Cleveland, tipping over that particular apple cart is a risk worth taking.
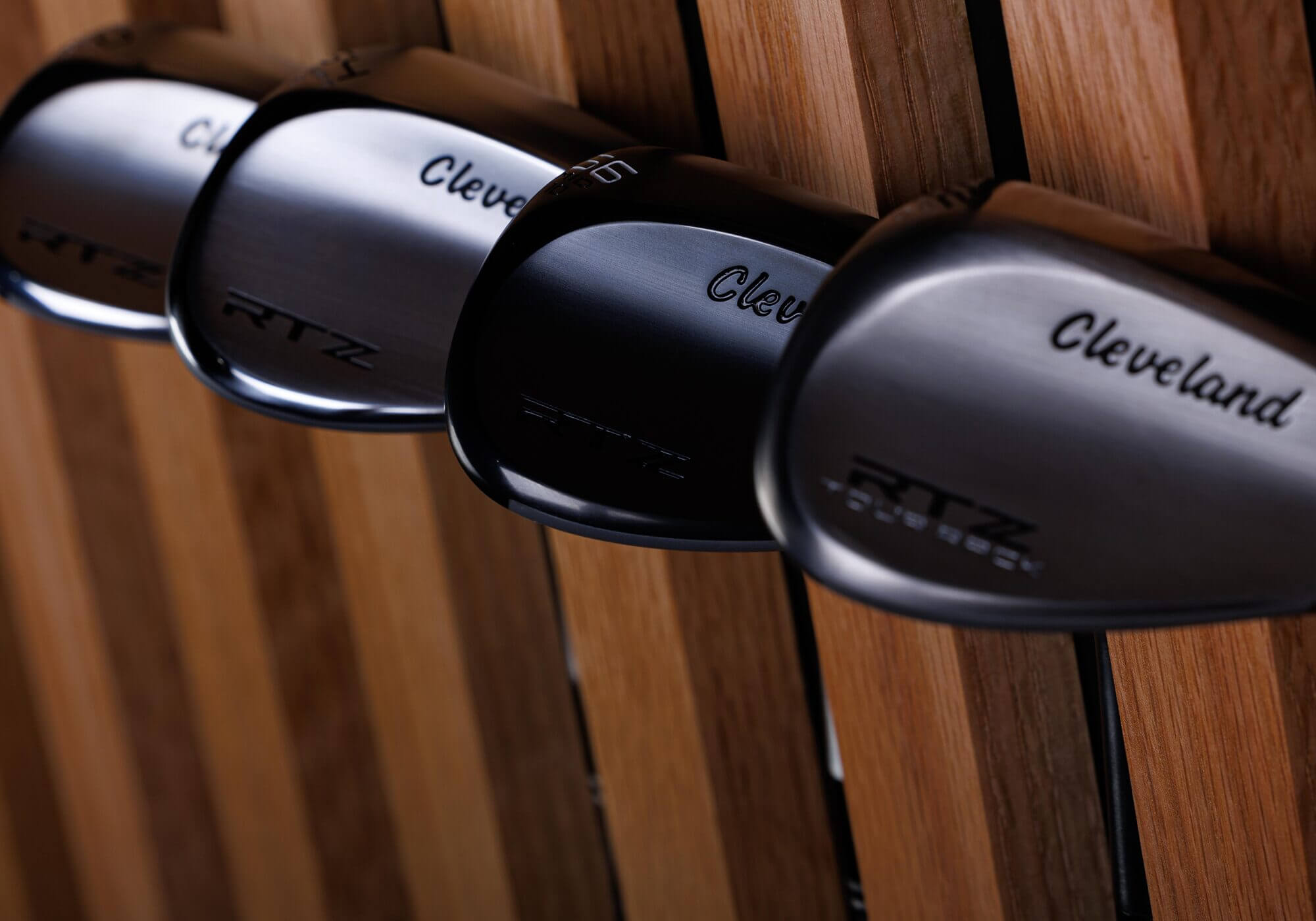
“You go into the unknown and if it blows up, it’s kind of on you,” says Smith. “It was very stressful because there were times when it wasn’t working and some tests failed. Looking back, though, we’re happy we went for it.”
With a wry smile, he added, “It’s also very easy to say that now.”
The post The Z-Alloy Story: Has Cleveland Golf Really Developed A Better Wedge Material? appeared first on MyGolfSpy.